Sous la surface : 11 essais en laboratoire pour les revêtements de protection
Laboratoire
Avant que nos revêtements ne soient appliqués sur des structures critiques à travers le monde, et même bien avant leur conditionnement et leur expédition, leur parcours commence en laboratoire.
Le laboratoire de SÄKAPHEN est le cœur battant de notre recherche et développement : c’est ici que naissent les revêtements sur mesure, que les formulations sont perfectionnées et que des essais approfondis sont réalisés sur les produits.
Notre objectif : fournir des revêtements de haute qualité, durables dans le temps et optimisés pour offrir des performances maximales et un excellent retour sur investissement (ROI). Nous collaborons étroitement avec nos clients à travers le monde pour proposer des solutions efficaces à chaque défi en matière de protection anticorrosion, contribuant à réduire les coûts de maintenance et à accroître l’efficacité opérationnelle.
Quand il s’agit de lutter contre la corrosion et la salissure, la performance est essentielle. Et derrière chaque revêtement haute performance se cache une série rigoureuse d’essais en laboratoire, conçus non seulement pour répondre aux normes, mais pour les dépasser. Voici les plus importants.
Essais mécaniques pour revêtements de surface
Un revêtement de protection doit être à la fois résistant et fiable, mais aussi suffisamment flexible pour absorber les chocs et les rayures, tout en assurant une excellente adhésion au support.
Parmi les essais mécaniques les plus courants, on trouve :
- Essai de quadrillage (cross-cut test) : une grille de coupes est pratiquée sur le revêtement, puis un ruban adhésif est appliqué pour vérifier s’il y a arrachement. Cet essai évalue directement la qualité de l’adhérence au substrat.
- Essai d’adhérence par arrachement (pull-off test) : cet essai mesure la force nécessaire pour détacher un cylindre (dolly) collé perpendiculairement sur le revêtement. Plus la force requise est élevée, plus l’adhésion est forte.
- Essai de résistance aux chocs (impact resistance test) : il simule des contraintes mécaniques soudaines, telles que la chute d’outils, afin d’évaluer la capacité du revêtement à absorber l’énergie sans se fissurer ni se délaminer.
- Essai d’abrasion selon la méthode Taber : non systématique mais pertinent pour évaluer la durabilité du revêtement. Un échantillon revêtu est soumis à l’action de roues abrasives en rotation, simulant une usure par frottement prolongé.
Essais chimiques pour revêtements de surface
La prévention de la corrosion se joue sur le terrain de la chimie. Dans des environnements exposés à des vapeurs acides, à l’humidité ou à des agents agressifs, la résistance chimique est cruciale.
Les essais chimiques les plus représentatifs incluent :
- Essai d’immersion sous lame : ce test permet d’évaluer la résistance du revêtement à la déformation et à l’altération en présence de liquides. Une substance liquide (eau, produit chimique) est appliquée sur la surface revêtue, recouverte d’une lame de montre pendant une durée définie, puis observée.
- Essai de vieillissement accéléré (weathering test) : réalisé en chambre climatique, il simule l’exposition à la lumière UV, à la pluie, au brouillard salin et aux variations de température. Il permet de prédire la durabilité du revêtement dans des conditions environnementales réelles.
- Essai d’immersion à température ambiante : ce test détecte d’éventuels défauts structurels du revêtement, comme les cloques, le gonflement ou la délamination, après une exposition prolongée à l’eau.
Essais spécifiques pour les revêtements haute performance destinés à l’immersion
De nombreux acteurs du secteur appliquent ces essais mécaniques et chimiques standards. Toutefois, pour les revêtements utilisés en immersion, notamment à l’intérieur de réservoirs ou de tuyauteries en contact avec des substances chimiques agressives ou des températures élevées, les exigences sont bien plus strictes. Les enjeux sont considérables.
Parmi ces essais avancés :
- Immersion dans l’eau jusqu’à 100 °C : réalisé dans de l’eau bouillante, cet essai vérifie la résistance du revêtement aux contraintes thermiques et à la pression hydrostatique. Il évalue la capacité de la couche à conserver son intégrité et son effet barrière dans des conditions extrêmes.
- Exposition à la chaleur sèche jusqu’à 200 °C : la chaleur sèche peut être aussi dommageable que l’humidité. Ce test évalue la résistance du revêtement à la fissuration, à la fragilisation, au farinage, à la dégradation et à la décoloration.
- Essai de résistance à la diffusion de vapeur d'eau : il mesure la capacité du revêtement à empêcher la pénétration de la vapeur jusqu’au substrat, prévenant ainsi la corrosion sous film, un phénomène critique dans les environnements industriels chauds et humides.
- Immersion chimique à haute température : l’un des tests les plus extrêmes du secteur. Le revêtement est immergé dans des acides ou des bases concentrés à des températures allant jusqu’à 100 °C pendant au moins 3 000 heures. Seuls les produits les plus performants conservent leur intégrité dans de telles conditions.
Pourquoi est-ce important ?
Sur le terrain, un revêtement n’a pas droit à l’erreur. Qu’il s’agisse de protéger un échangeur thermique, de revêtir un réservoir ou de préserver une turbine, il doit être parfaitement opérationnel dès le premier jour… et les suivants.
C’est pourquoi nous ne nous contentons pas de formuler des produits performants. Nous les mettons à l’épreuve.
Contactez-nous pour en savoir plus sur l’approche de SÄKAPHEN en matière de tests en laboratoire et sur la manière dont nous pouvons répondre à vos besoins spécifiques.
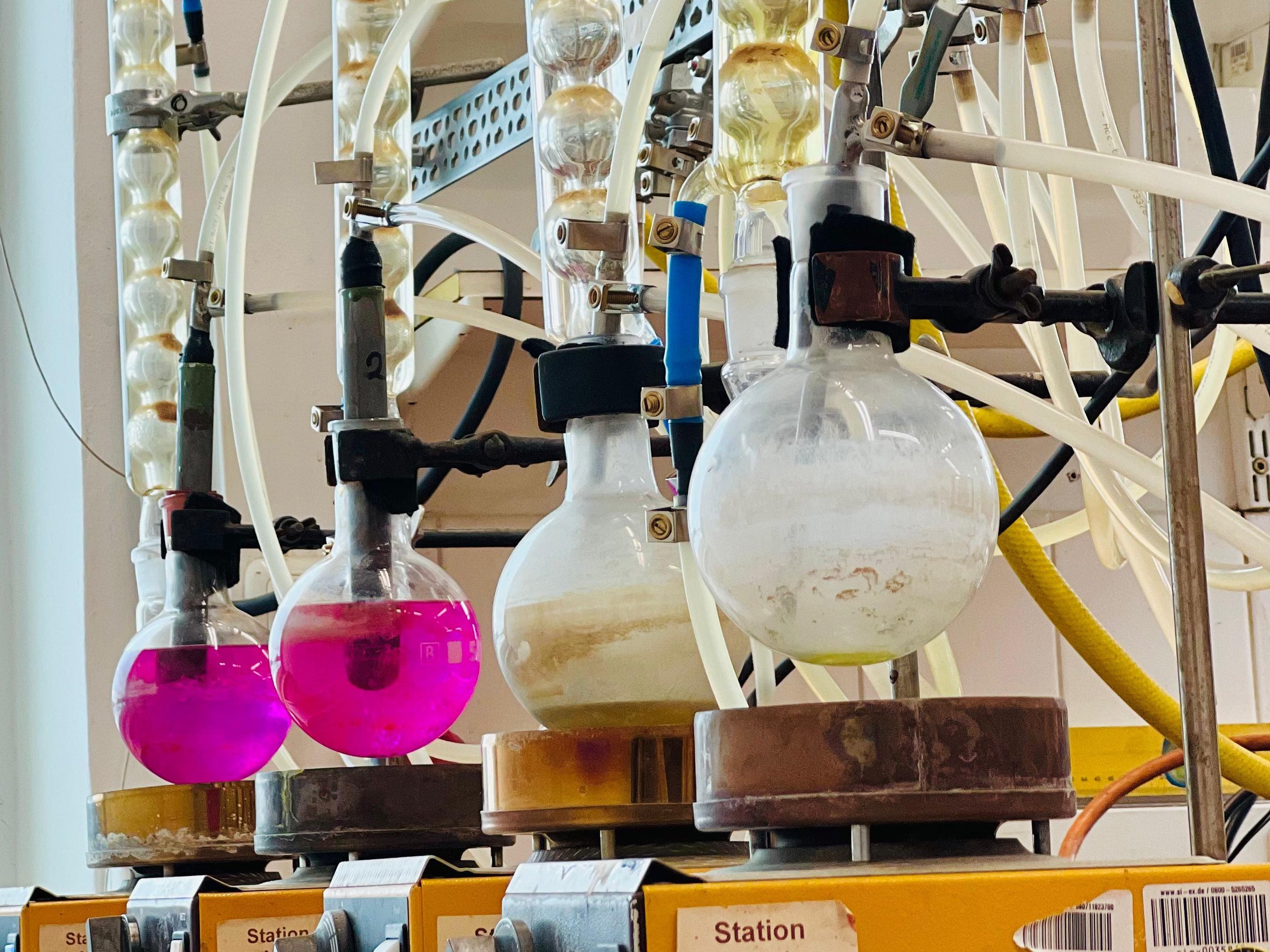
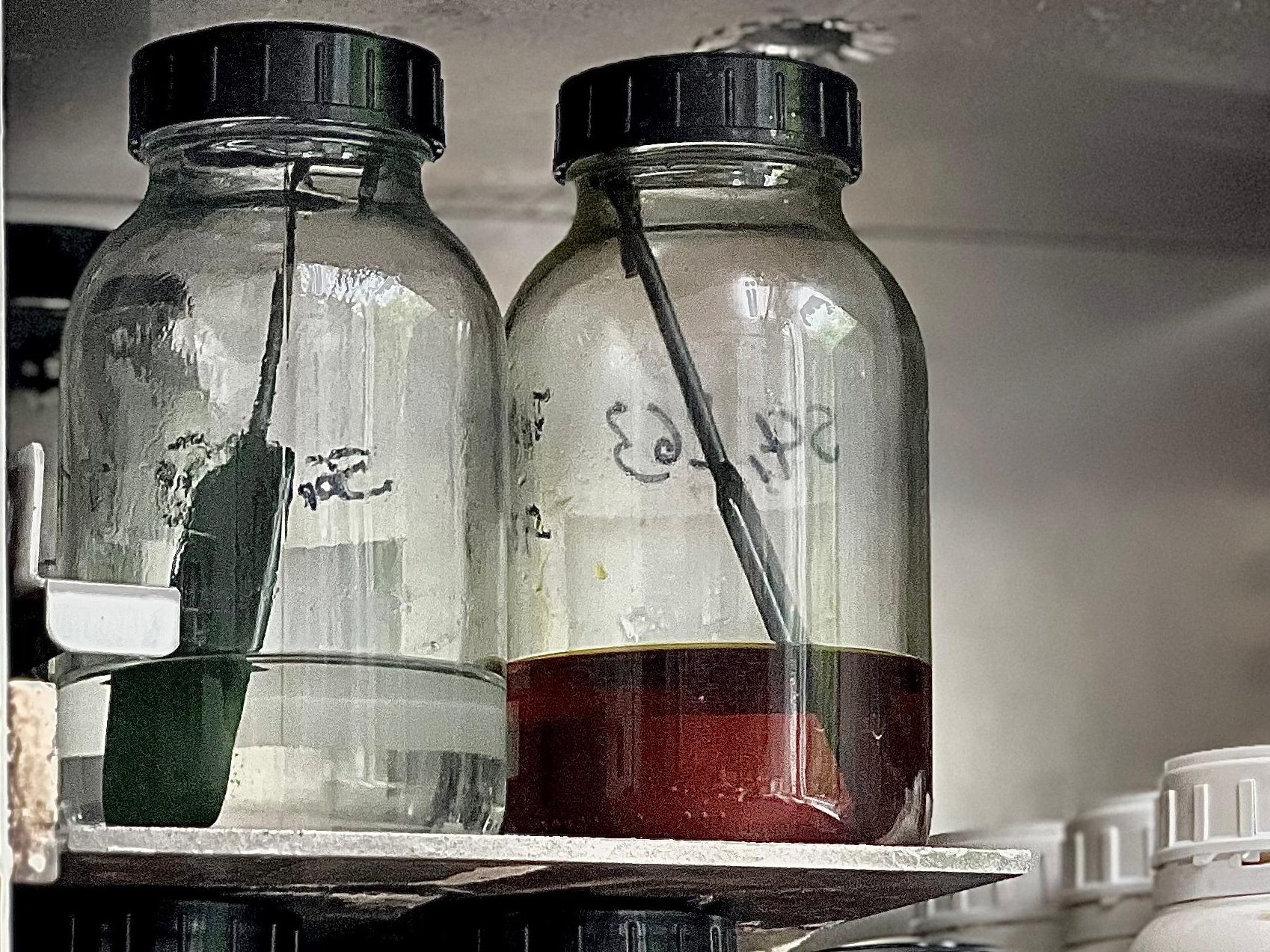
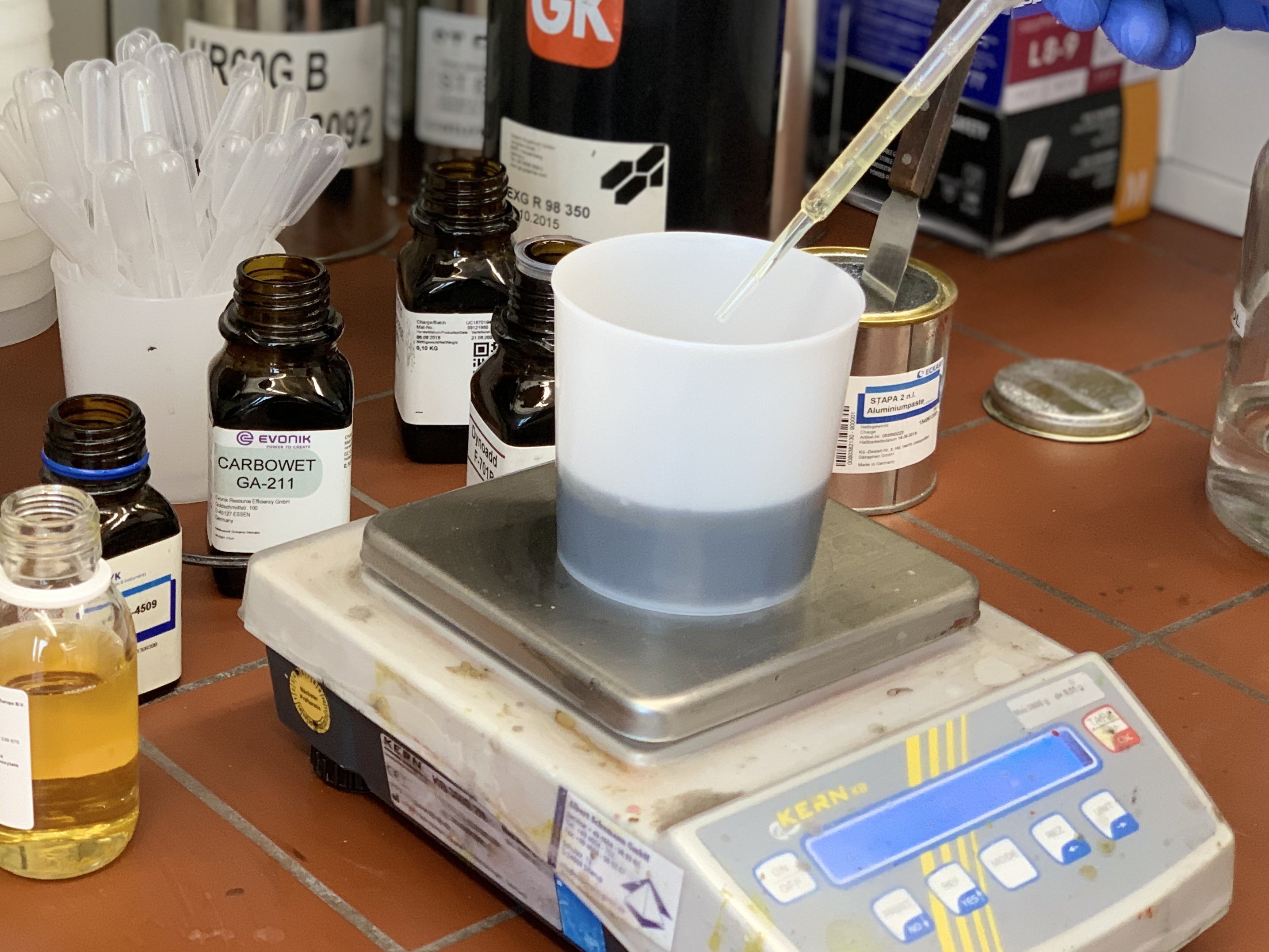
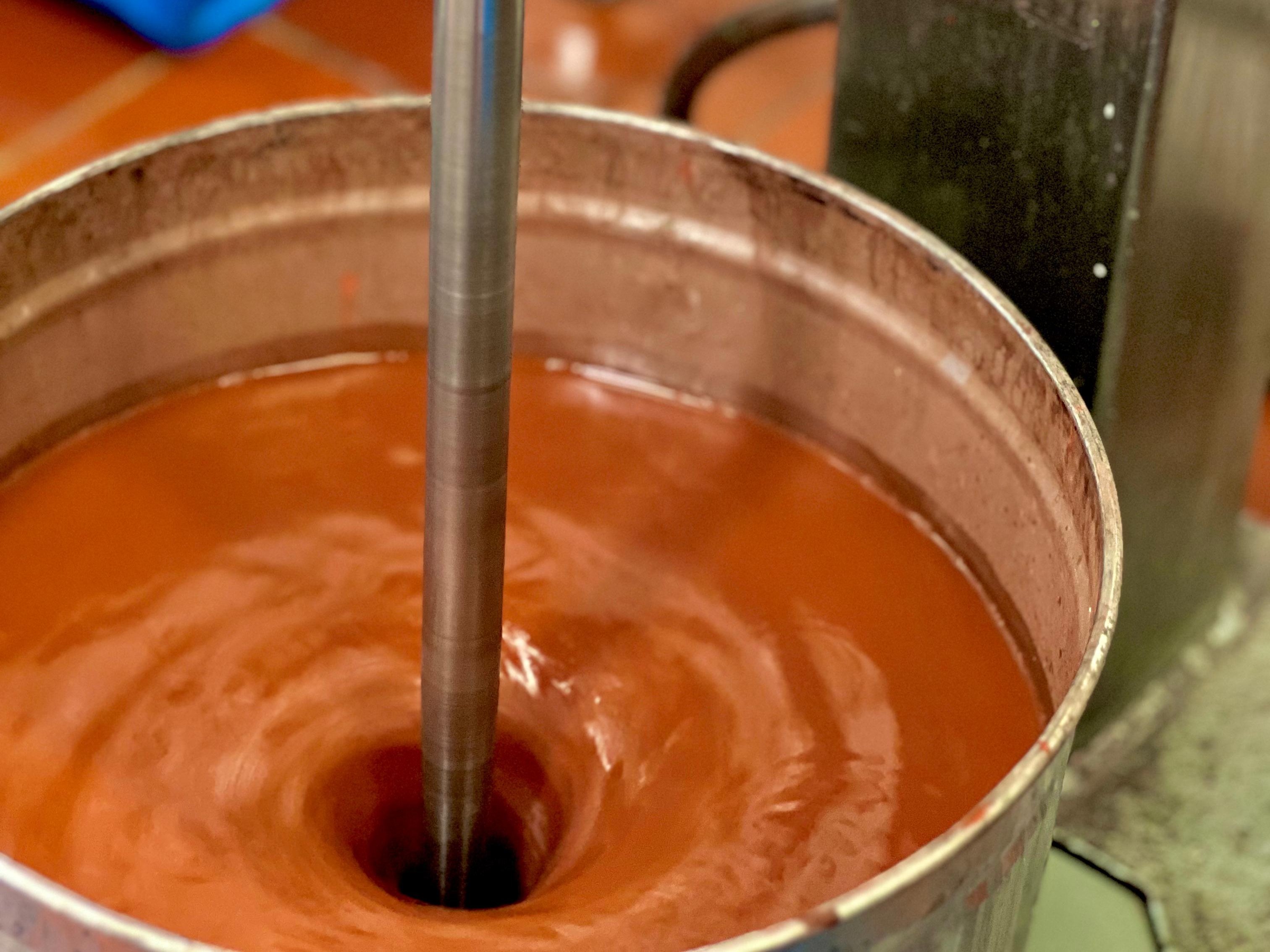

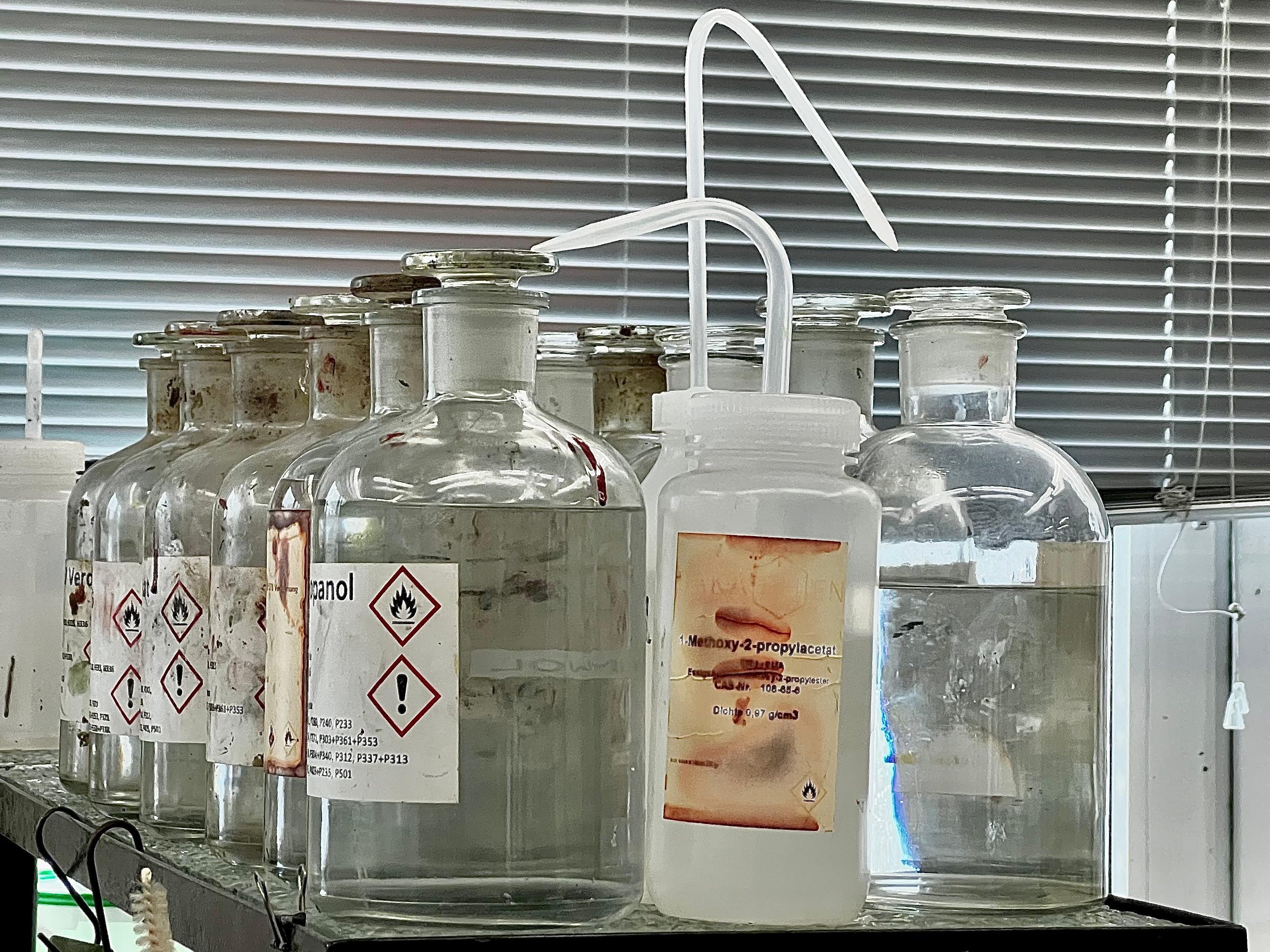