7 Things You’ve Always Wanted to Know About Lining U-Tubes in Heat Exchangers
Si 14 EG
7 Things You’ve Always Wanted to Know About Lining U-Tubes in Heat Exchangers
Why should you line U-tube bundles? Is that even possible? How can an expert company help? We’re here to answer.
Heat exchangers are vital components in countless industrial processes, enabling efficient thermal energy transfer between fluids. Among the various designs available, the U-tube bundle heat exchanger is common due to its ability to handle significant thermal expansion and its relatively simple design, which requires only one tube sheet. In this configuration, a bundle of tubes, each bent into a U-shape, is housed within a shell. Typically, one fluid flows through the tubes (tube-side), while another flows outside the tubes within the shell (shell-side).
1. So why do U-tubes need lining in the first place?
U-tubes in heat exchangers carry fluids that can be highly corrosive, abrasive, or prone to fouling. Over time, this exposure leads to:
- Corrosion: chemicals in the fluids eat away at the tube walls.
- Erosion: high-velocity flows wear down the metal.
- Fouling: deposits form inside the tubes, reducing efficiency.
While choosing tubes made of corrosion-resistant alloys is option one, it can be very expensive or sometimes not technically feasible. Internal lining offers an alternative path, protecting a cost-efficient base material, such as carbon steel, against corrosive fluids to prevent leaks, maintain efficiency and extend the exchanger’s life.
2. Why is coating U-tubes’ internal surfaces difficult?
Lining straight tubes? No problem. Lining U-tubes? That’s a different challenge. Here’s why:
- Tight bends: curves make it more difficult for the coating material to adhere evenly. However, consistency is vital to avoid a range of problems, from coating failure to cracking and baking issues.
- Build quality: lining U-tube heat exchangers takes more time for application, which means there are higher chances for the material to become sticky and hinder the product’s flow out of the tube ends. Therefore, it is also important that the tube ends are not “over-expanded” with a deep groove.
Plus, let’s not forget the issues typical of any heat exchanger:
- Surface preparation: the inside surfaces should be impeccably clean and adequately prepared for the lining to stick. However, doing this reliably deep inside narrow, bent tubes can be a challenge.
- High lengths and low diameters: getting lining material deep into long tubes is not easy.
- Thickness issues: some areas may get too much coating while others don’t get enough.
- Adhesion issues: if the lining is applied and, therefore, polymerized unevenly, it delaminates in between the layers, leaving the tube unprotected.
3. How can you even check lining results?
Checking coating results is another key issue. Videoscopes should be used to “snake down” the tubes and visually inspect the surface. However, looking around the corner into the U-bend is impossible. That’s yet another reason why excellent workmanship is critical in lining these plants. Moreover, detecting tiny pinholes might require specialized electrical inspection tools (Holiday detectors) adapted for small-diameter tubes. Finally, measuring the Dry Film Thickness (DFT) is crucial. Reliable measurements can be obtained at a distance of 20 cm from the tube ends, where gauges can access them.
4. How to make sure this lining process is done right?
Specialist know-how is key here. A company specializing in tube lining operations is the go-to partner, with its deep knowledge, proven expertise, tried and tested products and processes and excellent workmanship. High care is of the essence for the success of such a complex operation.
5. So what does the U-tube bundle lining process look like?
The most typical method is flooding application. These are the steps required:
- Surface preparation: thorough internal cleaning to remove dirt, rust, residues or old coating layers.
- Setup: the tube bundle is positioned on rollers to allow rotation.
- Lining application:flooding the liquid lining into the tubes and draining at a controlled rate. The bundle is then rotated, and the operation is repeated until a uniform film thickness is achieved.
- Baking: performed with heat-cured coating products. This entails a further challenge because, whereas hot air is forced into the tubes with other types of heat exchangers, a small tweak is required here (which will remain a well-kept secret, sorry!).
- Inspection: checks performed with specialized tools.
6. What happens if U-tube lining is done incorrectly?
A poor-quality lining can cause coating failures (the lining peels or cracks, exposing the metal) and uneven protection (some areas remain vulnerable to corrosion), leading to reduced heat transfer, lower equipment efficiency and, therefore, higher operating and maintenance costs.
7. Is this a standard, everyday procedure?
Absolutely not! Lining the inside of U-tubes is a highly specialized servicethat calls for experienced professionals and advanced equipment. With the right expertise and tools, this complex task can be tackled with precision and reliability, ensuring excellent results and long-term performance.
That’s why relying on an expert partner like SÄKAPHEN is even more crucial. Let’s talk!
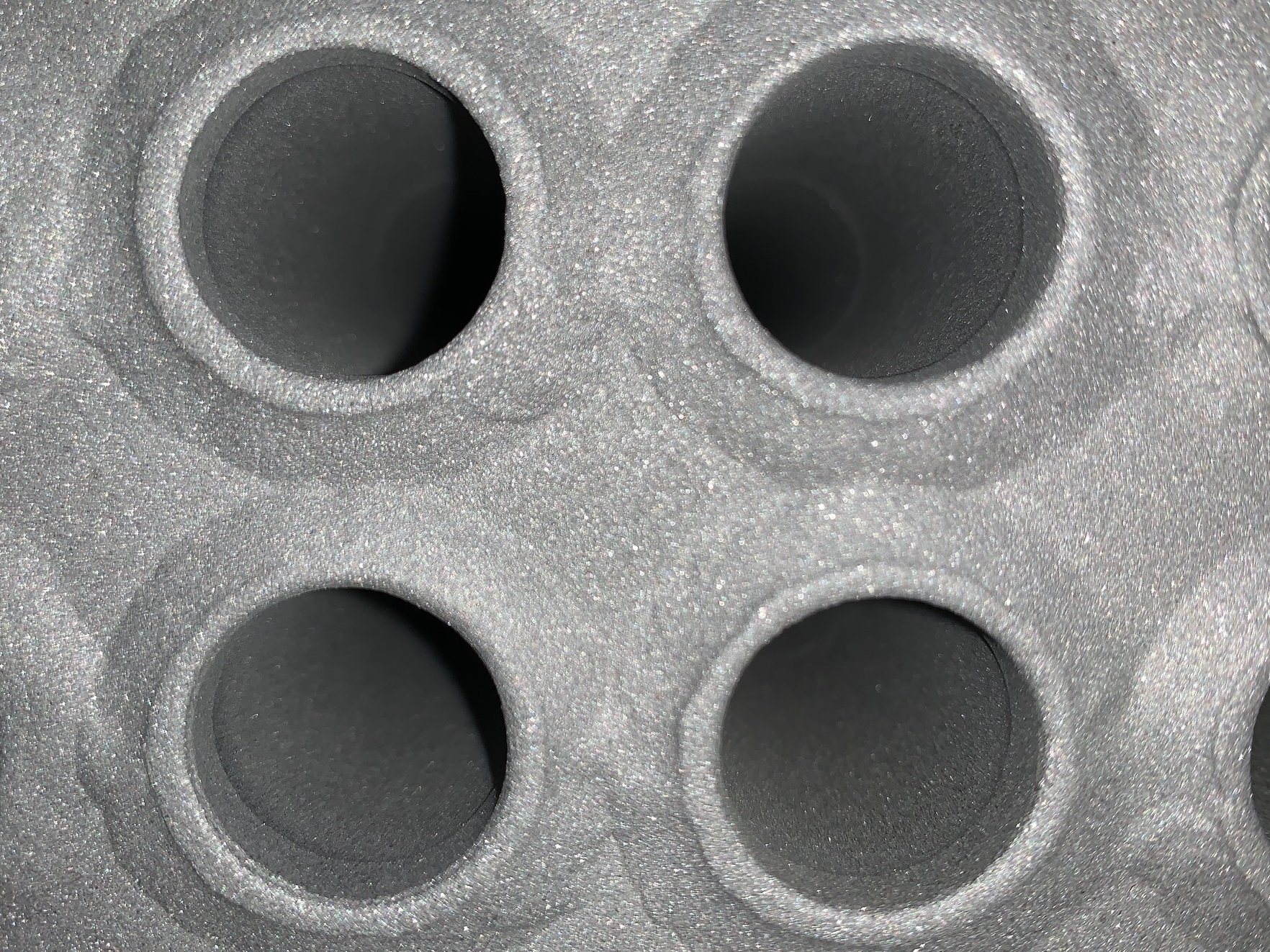



