Case study: protecting heat exchanger pipes, no matter their length
Si 57 E & Si 57 E/RE
Preventing corrosion, protecting HE tubes’ surfaces and ensuring long-term reliability and safety with SÄKAPHEN’s coatings and application processes
As soon as a special request from a major chemical manufacturer landed on our desks, we knew it would entail an unprecedented challenge for us. That is why we immediately chose a best-in-class product from our heat-cured linings range and turned to one of our trusted authorized applicators.
Challenging specifications
Customer: a major multinational company specializing in chemical engineering
Items to be coated: 86 high-pressure pipes for a large-sized heat exchanger
Length: 15 meters each
Material: special alloy
Mediums in contact: aggressive cooling water (shell side) and corrosive solvent over 100 °C (tube side)
The customer chose to rely on us because it was very satisfied with the durability of the system’s old pipes, which had been operating for 20 years, also thanks to our protective linings.
The tubes’ length, of course, represented the most significant challenge of this project. The aggressive mediums in contact with the pipes’ substrates also called for careful consideration. Finally, the customer insisted on an even 200-micron DFT (Dry Film Thickness) value along the whole tubes’ length as consistent heat transfer is critical – quite a challenging result when hand-applying the coating.
SÄKAPHEN’s solution
1. Above-average application skills
Only one applicator in Europe could successfully tackle this challenge: Romania-based AlpAccess. Our trusted partner’s exceptional application skills ensured we could treat such long pipes while maintaining very high quality standards.
As always with SÄKAPHEN, the pipework treatment process included the following steps:
- Preliminary analysis and technical consultancy
- Surface preparation (grit blasting and cleaning)
- Coating application until the achievement of the ideal DFT (dry film thickness) and curing
- QC, testing, and preparation of the required documentation.
2. High-quality products
SÄKAPHEN offers a wide range of coatings and linings to protect the surfaces of pipeworks and ductworks against a numerous products and mediums, including, for example, blast furnace gases and fumes and other gaseous and liquid products found in refineries, power generation, chemical, petrochemical industries and general industrial processing.
In this case, the 86 pipes were coated as follows:
- no tube-side lining (corrosive solvent over 100 °C)
- shell-side coating with SÄKAPHEN Si 57 E (aggressive cooling water)
We selected Si 57 E because it is a high-quality, hydrophobic, single-component, epoxy-phenolic based, thermosetting, heat-cured lining. It is self-priming and developed for direct-to-metal application. It is chemically resistant to various substances ranging from strong alkalis to weak acidic media, salt solutions, greases, oils and gases and all types of cooling water, including brackish, river, seawater and deionized water. Its film surface is hard elastic with exceptional hydrophobic properties, preventing caking, fouling and incrustation. It has a formaldehyde concentration level of less than 0.1%.
Final results
The customer was very pleased with the project’s results. These included as follows:
- High-level corrosion prevention
- Optimal prevention of caking, fouling and incrustation
- Excellent overall protection of the surfaces of the heat exchanger’s tubes
- Long-term plant efficiency and reliability
- Outstanding ROI (return on investment)
- Maximum operational safety.
SÄKAPHEN: your ideal partner for corrosion protection
We work alongside our customers worldwide to provide the best solutions to all their corrosion protection challenges, ensuring reduced maintenance costs and increased operational efficiency.
Contact us today to discuss your next project, no matter how complex!

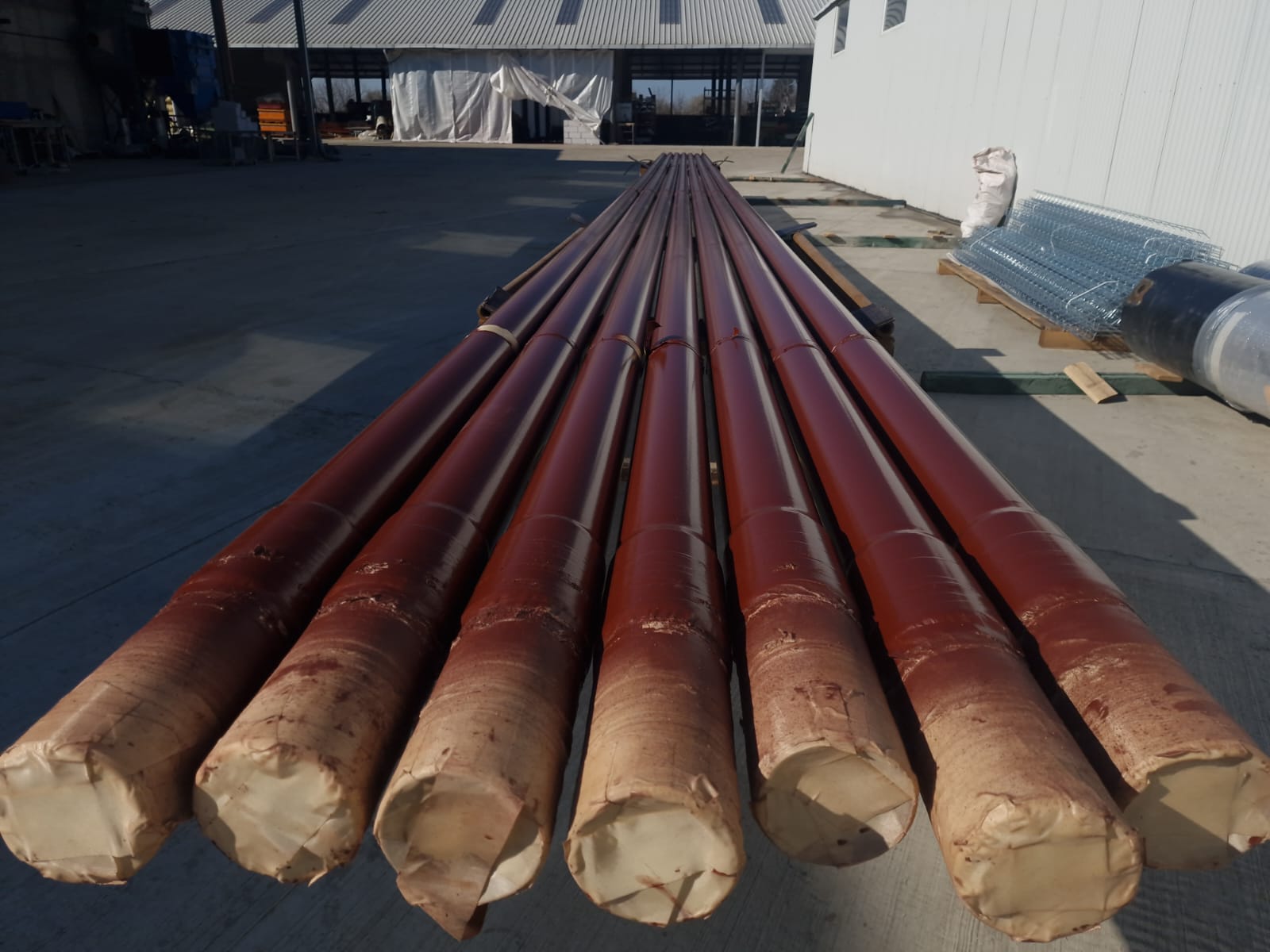

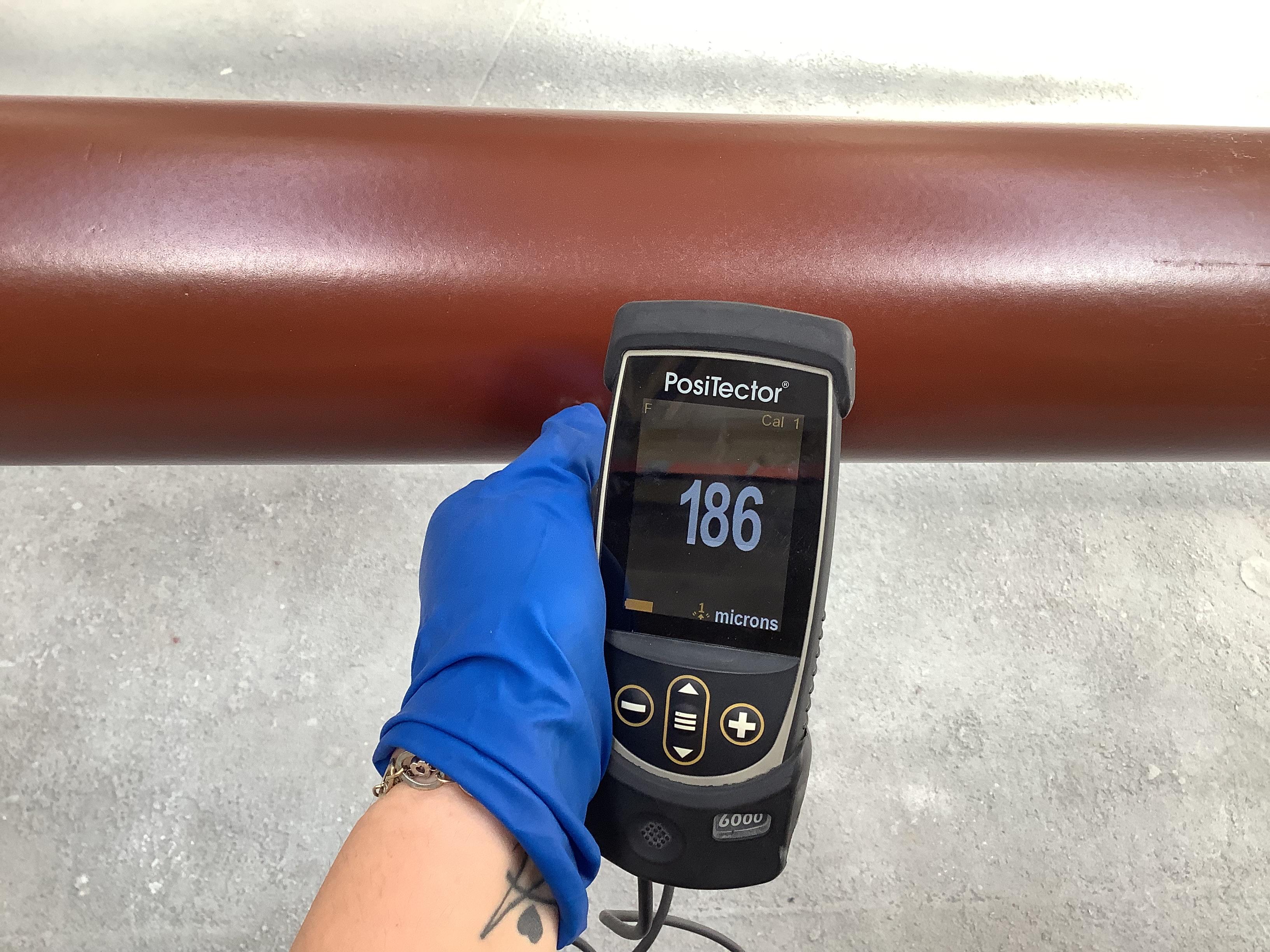

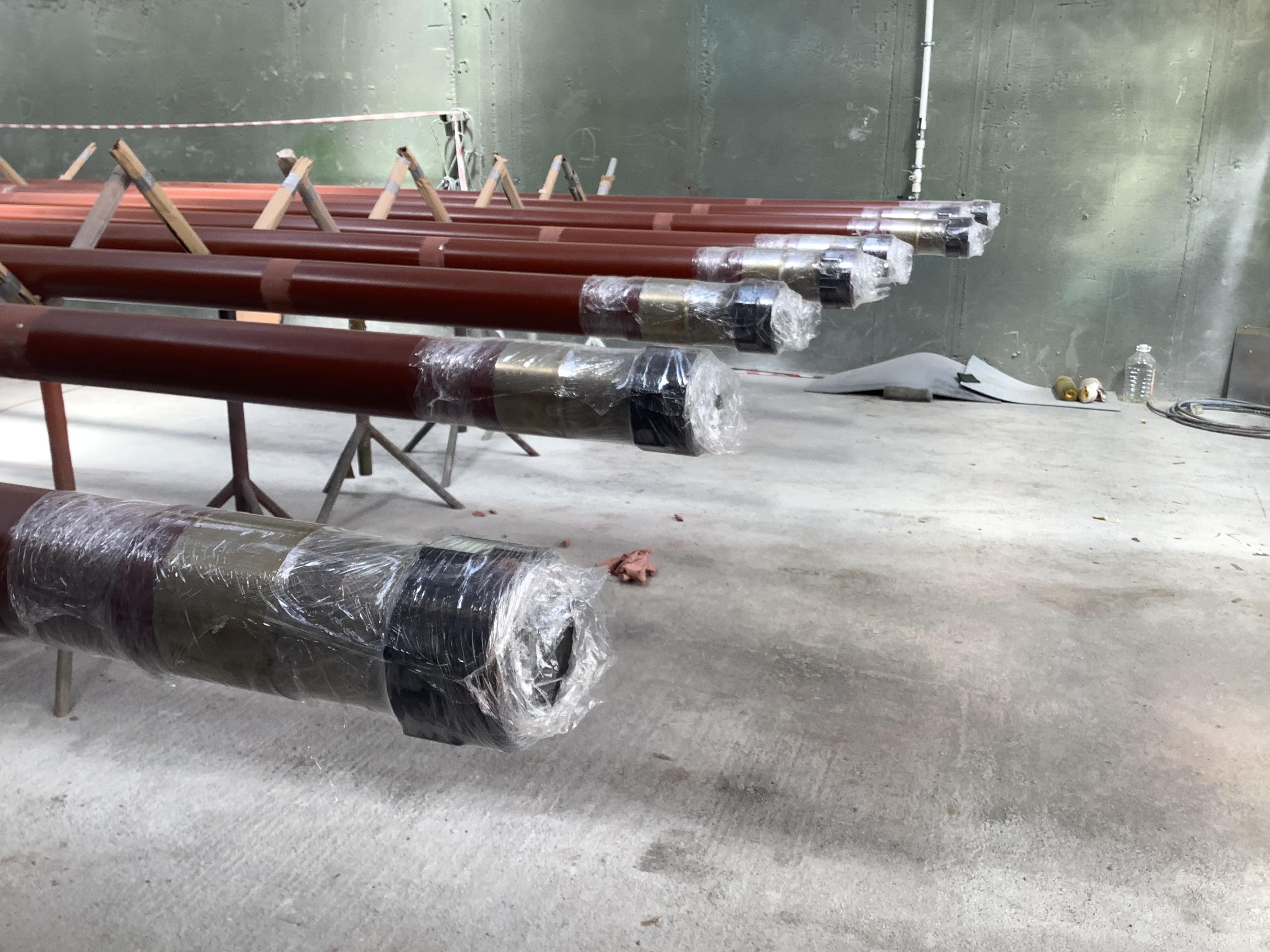
