A Day in the Life of a Coating Inspector
SÄKAPHEN Si 14 EG
Can you apply SÄKAPHEN’s coatings in your workshop? Do you need to become an Authorized Applicator? Can we carry out an audit at your site? We will answer these and more questions with the exemplary story of a successful partnership. Because a high-quality lining only results from a top-quality product combined with a top-quality application.
What started as a one-off on-site audit conducted by SÄKAPHEN at the premises of a Thai user has soon become a synergic collaboration between a coating manufacturer and one of its newest partners.
When company Trepax approached us, it had already selected our Si 14 EG heat-cured phenolic product for one of its lining projects. In general, SÄKAPHEN’s baked phenolics are only applied by Authorized Applicators to ensure the high quality and performance of these high-end linings. However, Trepax wasn’t sure about immediately becoming an Authorized Applicator. Our Commercial Director Christoph Fischer-Zernin, a Certified NACE Inspector – Level 2 and in charge of SÄKAPHEN’s business development, offered the perfect solution: performing an audit on Trepax’s application capabilities, processes and results. Thanks also to the prior experience of one of Trepax’s project managers in the field of heat-cured phenolic coatings, it was a great success, thus starting a hopefully long-standing partnership between these two companies.
Thinking back at that experience, Fischer-Zernin decided to reflect on SÄKAPHEN’s auditing procedures and what it takes to succeed in them.
When you’re approached by a party who wants to apply your well-known heat-cured coatings, what are their initial thoughts? And what is your initial approach?
Usually, the approaching party (EPC/Contractor) has an application request from an existing or potential client for one of our products, likely a baked lining. As SÄKAPHEN is well known for the excellent performance of its coatings and its carefully selected applicators for high-quality operations, the inquiring party is curious to know:
- as an EPC, where the nearest Authorized Applicator is located;
- as a contractor, what are the commercial and technical prerequisites to becoming a SÄKAPHEN Authorized Applicator.
First, we name a geographically fitting Authorized Applicator to the EPC. If no Authorized Applicator is available despite our vast global partner network, and the EPC can recommend a reliable applicator or if there is a general interest by an applicator in broadening their service portfolio, we investigate if this is going to be a one-time application or if the inquiring party is interested in a long-term relationship.
In the past, we did not focus on one-time applications. However, since baked coatings and linings are becoming more popular again, we now also support these jobs, especially if an applicator already has experience with other baked products, primarily liquid.
Once this is clarified, we check whether the applicator fulfils our technical requirements regarding the equipment needed for surface preparation, coating application and baking. As one of SÄKAPHEN’s signature application processes is the tube-side lining of heat exchangers, verifying if equipment suitable for such an application is available at the inquiring party’s site is also essential.
Finally, we plan an on-site audit. This applies to both one-time applications and long-term partnerships.
When preparing for an audit, what are the preliminary questions you ask even before getting on-site?
As mentioned before, we check if the applicator fulfils our technical requirements regarding the equipment needed for surface preparation, coating application and, above all, baking prior to any inspection/audit on site. This saves costs and time at both ends. Usually, we share the application procedures and baking charts with them and, in return, receive detailed information about the equipment available. As this establishes a continuous exchange of verbal and written information, many questions come up from both sides, which as a “side-effect” helps everyone make a good impression on each other. Therefore, when the audit starts, both parties know each other well and can focus on the core task: to see if all is set and ready to apply SÄKAPHEN products to the highest standards. In its more than 70 years of experience, SÄKAPHEN has repeatedly confirmed that a high-quality lining results from a top-quality product combined with a top-quality application. One does not work without the other.
What do you focus on at the very beginning of your inspection? What contributes to making a good first impression on you?
Having done multiple audits and on-site inspections over my last 14 years at SÄKAPHEN, I have noticed that the joint travel preparations to the audit’s location already reflect the other party’s workmanship degree. Because if processes are structured, the company is structured, too. And that also means that a project such as an audit will likely run smoothly – as everyone involved hopes, of course.
At the location, we look at cleanliness and workplace structures. Having a workshop ourselves, I can walk through a site and, while looking around, already assess at first glance if the audit is going to succeed. Interestingly enough, other people from the industry have shared the same experience with me.
How do you then conduct the actual audit, and with what instruments?
The actual audit can be done in two ways.
If the job only involves the spray application of a SÄKAPHEN baked coating product, I simply run through the application process on sample plates, from surface preparation to multi-layer application and baking, including intermediate and final bakes. I look at the quality of the application operation, the fulfillment of application guidelines, the quality assurance and control and its documentation. The latter is particularly interesting as although the documentation’s scope is pretty much standardized in the industry, everyone uses their own format, thus always creating the occasion for a fruitful exchange.
If the customer wants to apply a SÄKAPHEN lining inside heat exchangers, we are usually looking at a long-term relationship. In this case, we do all the above to verify that the application equipment works correctly. In addition, we supervise a trial or actual application process of a SÄKAPHEN product inside a heat exchanger, especially because flooding does sound very easy – but ask any SÄKAPHEN applicator: we all had to learn it!
In both cases, this is not a control performed with a critical or negative approach but rather a verification that the applicator is aware of the challenges entailed in applying baked linings.
How do you like to end an audit?
Obviously, we prefer this to result in a successful audit with a happy partner, confident in their skills and level of quality and knowing they can call us anytime in case of challenges or technical requests. More practically, at the end of an audit, about three larger sample pieces should have successfully been cleaned, blasted, coated, baked and QC’ed, including proper documentation.
What advice would you give to any applicator intending to use SÄKAPHEN’s baked products? What can you recommend to make sure the application is a success?
It is always recommended to read the instructions provided carefully. This should be followed by an internal discussion, also asking us as the issuer: it is, in effect, a toolbox meeting – massively important for any project, whether with SÄKAPHEN or any other manufacturer. Other than that, excellent workmanship is paramount. During my NACE CIP training many years ago, the importance of workmanship was the first lesson I was taught. After more than a decade in the industry, I now know why and fully agree. Finally, I recommend calling us in case of any issues. One of our partners or we will undoubtedly have experienced the same problem and have the right answer. SÄKAPHEN is not only about a product with a related application technology, but rather a solution against corrosion and fouling, including a trustful exchange amongst the partners in our network.

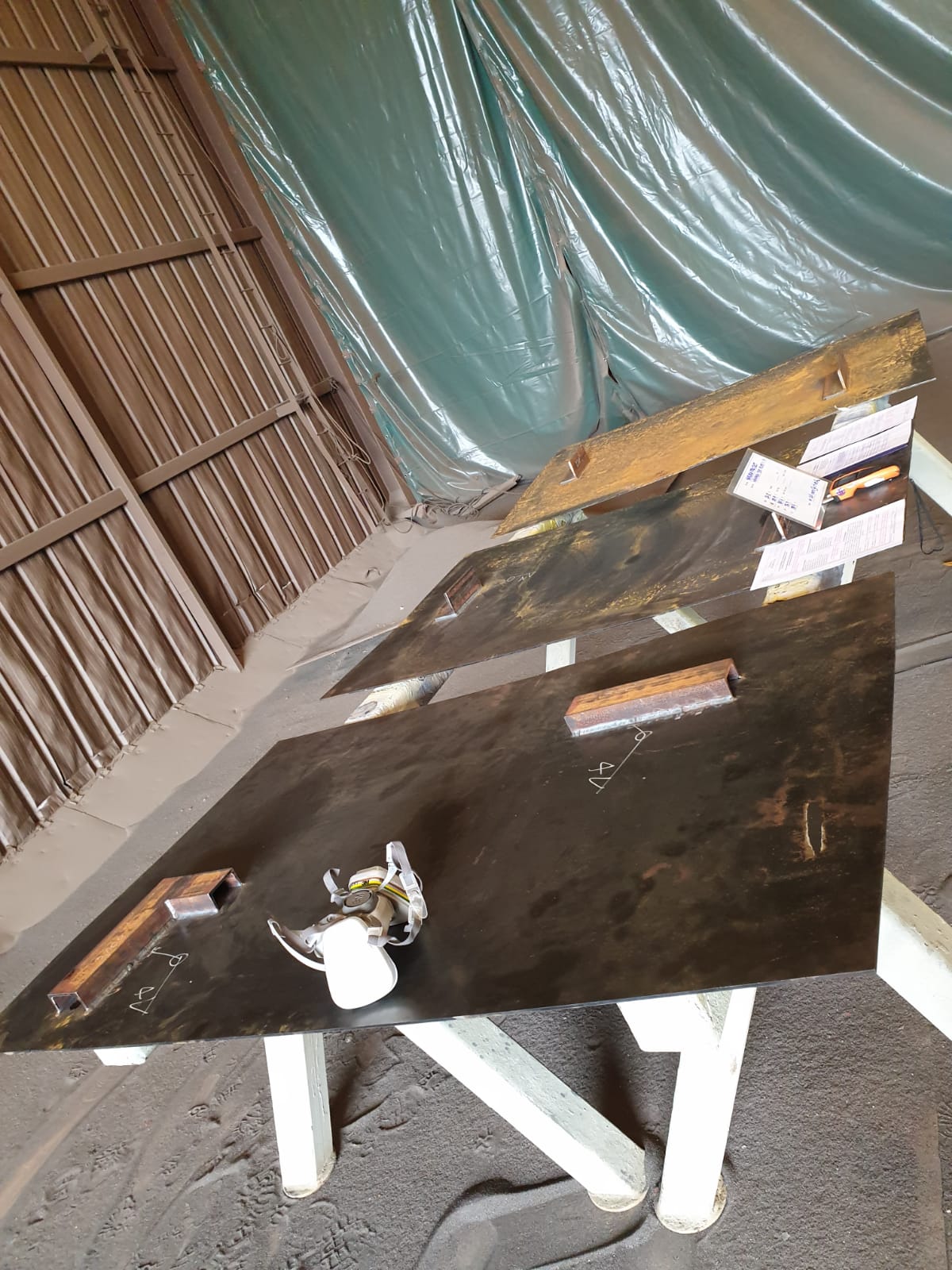


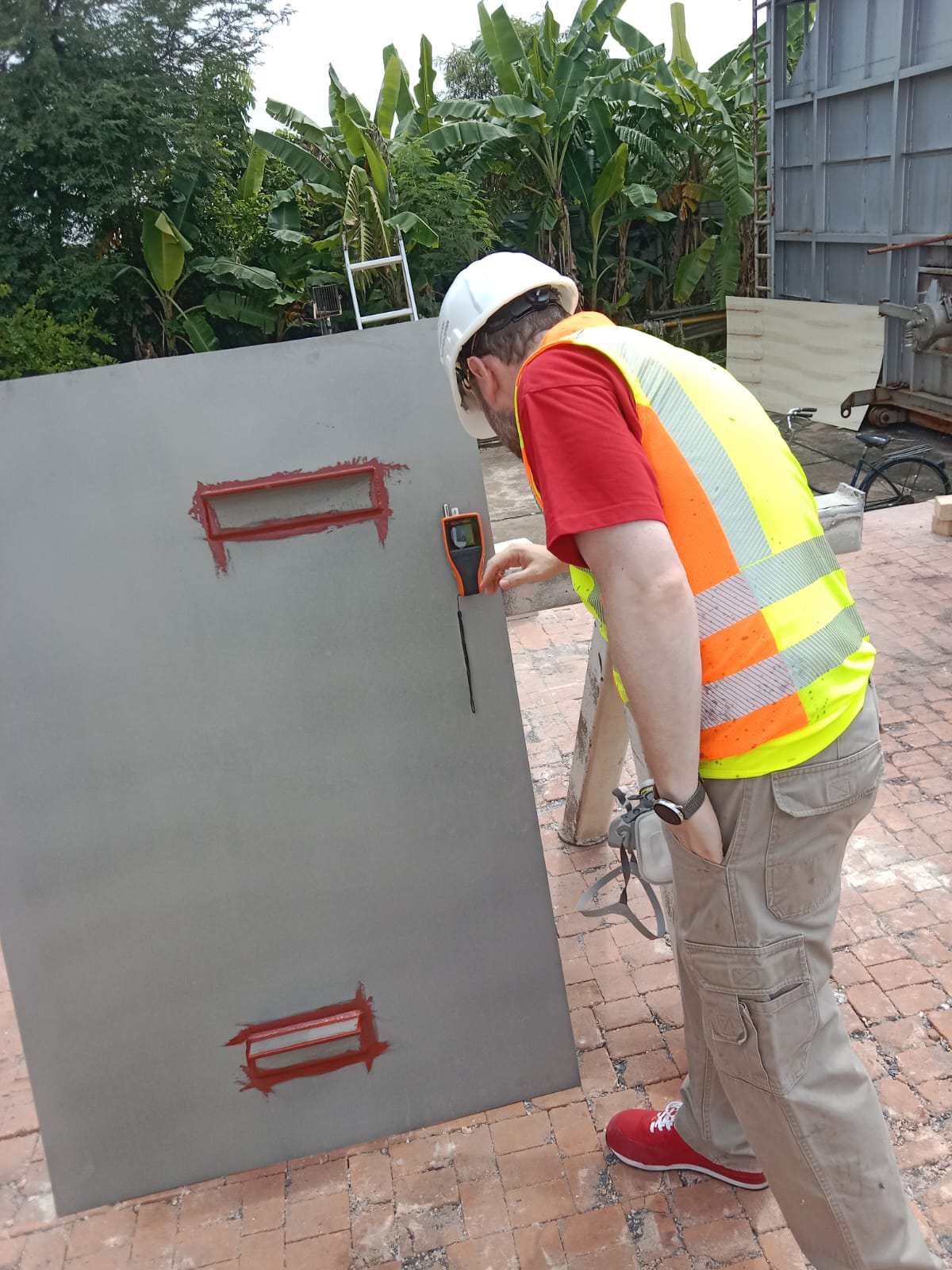
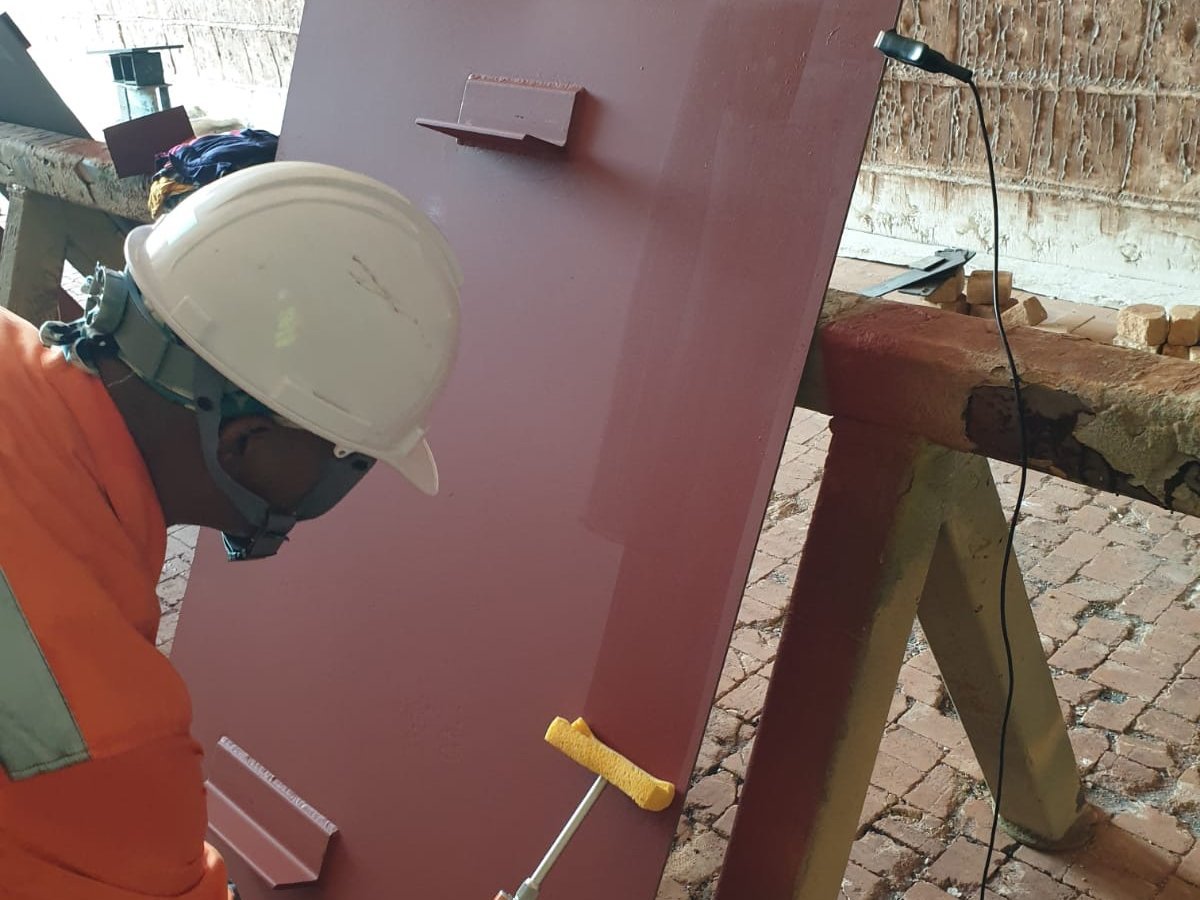
